Grinding process
From a long experience of design and construction of double roll presses,
These machines can crush materials of variable size range. The material fed between the rollers is ground and comes out as friable flakes. Depending on the flowing of the product and its bulk density, in some cases a gravity feed system is sufficient to feed the rolls.
SAHUT‐CONREUR
has developed a range of roller press specifically adapted for grinding application.These machines can crush materials of variable size range. The material fed between the rollers is ground and comes out as friable flakes. Depending on the flowing of the product and its bulk density, in some cases a gravity feed system is sufficient to feed the rolls.
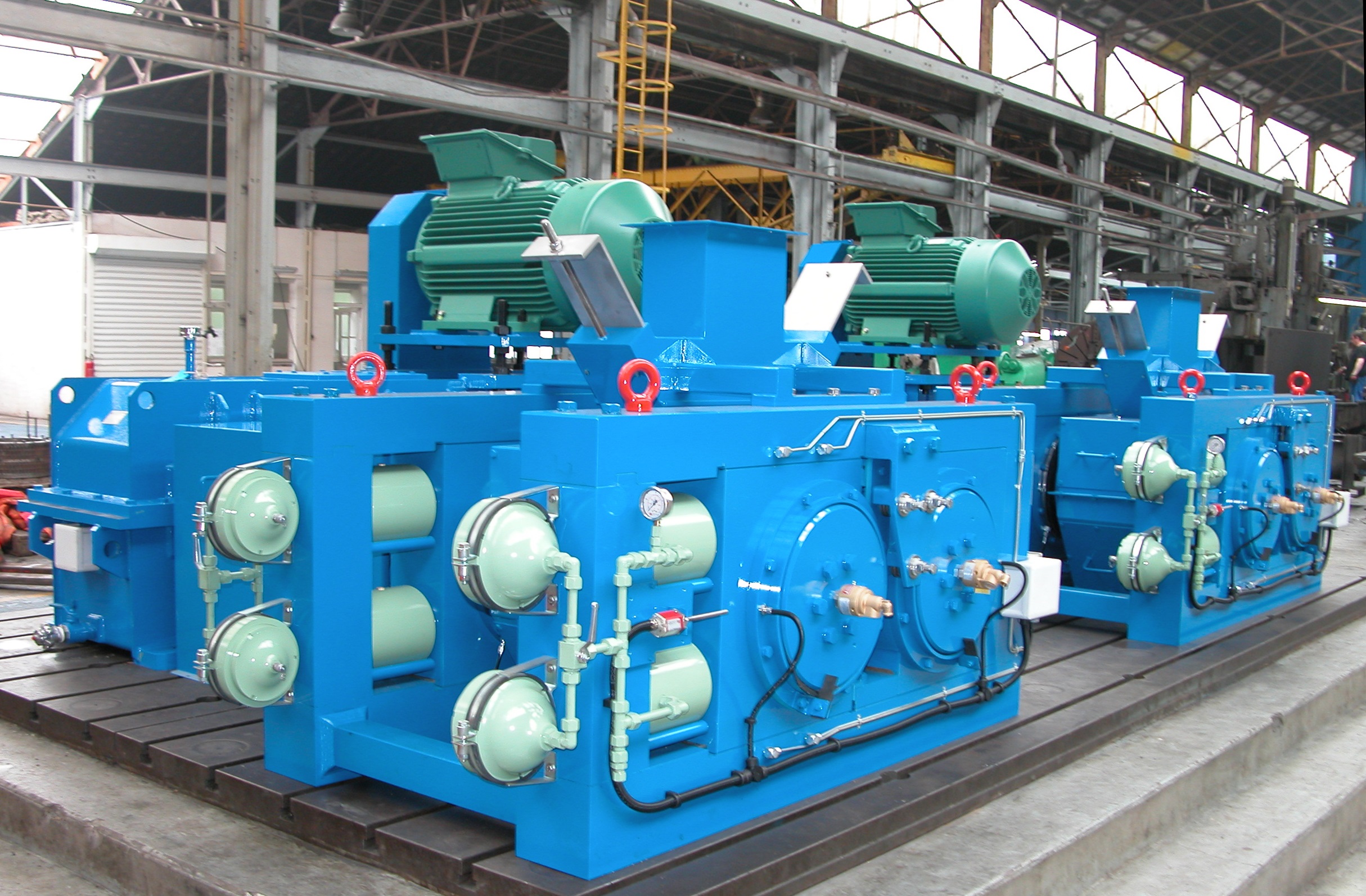
For materials with low density and critical flowing, the feeding of the rolls must be ensured by a
pre‐densification screw
(force‐feeder). In most cases, a single pass through the roller press is sufficient to obtain the
desired particle size reduction.
If the final product requires an extremely fine particle size or if the particle size range is very
accurate, a screen or an
air classifier must be installed after the roller press. Oversized particles are returned to the
roller press for a new
grinding pass.
Compared with traditional techniques, the use of this process means:
Compared with traditional techniques, the use of this process means:
- Energy savings up to 50% for some materials.
- Throughput increases of crushed end‐product from 30 to 100% when the process is fitted into an existing grinding circuit.
- A cost decrease of production and low wear maintenance of these equipment.
- A low noise operation.
- A low space required.
- High availability.
- No contamination of the product.
Typical flowsheets for TIO2 grinding plants
The raw material used during the manufacture of titanium dioxide pigments, often issued of ores as Rutile (R) or Anatase (A), undergo calcination treatments before to be finely grinded. This grinding process is very important due to its influence on the next steps of process but also because of energetic and maintenance costs. Since several years, the roller press has been introduced in this grinding process to replace pendulum mills or hammer‐mills.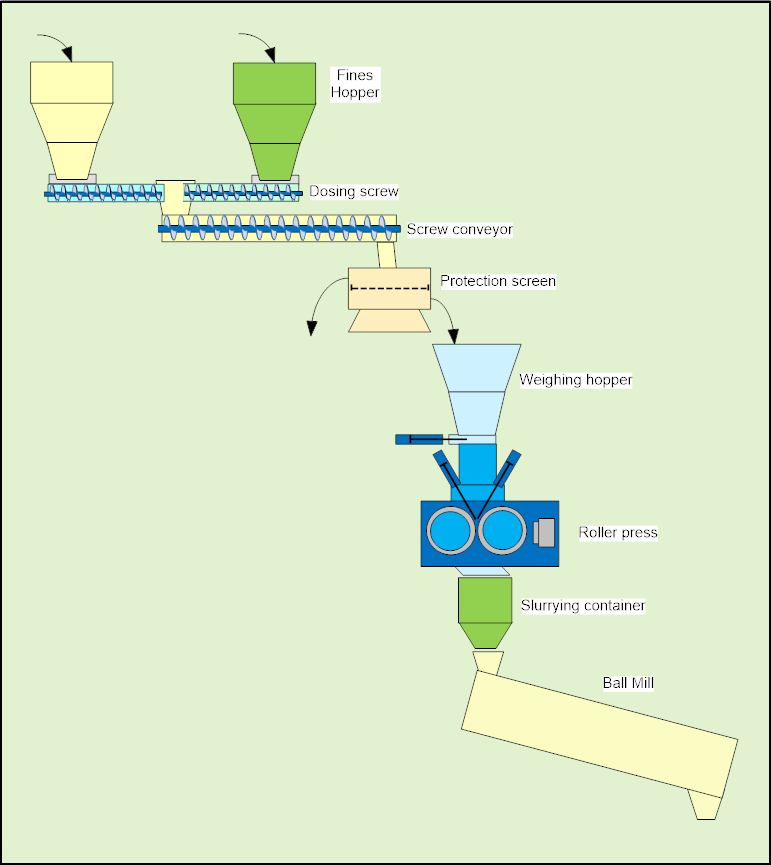
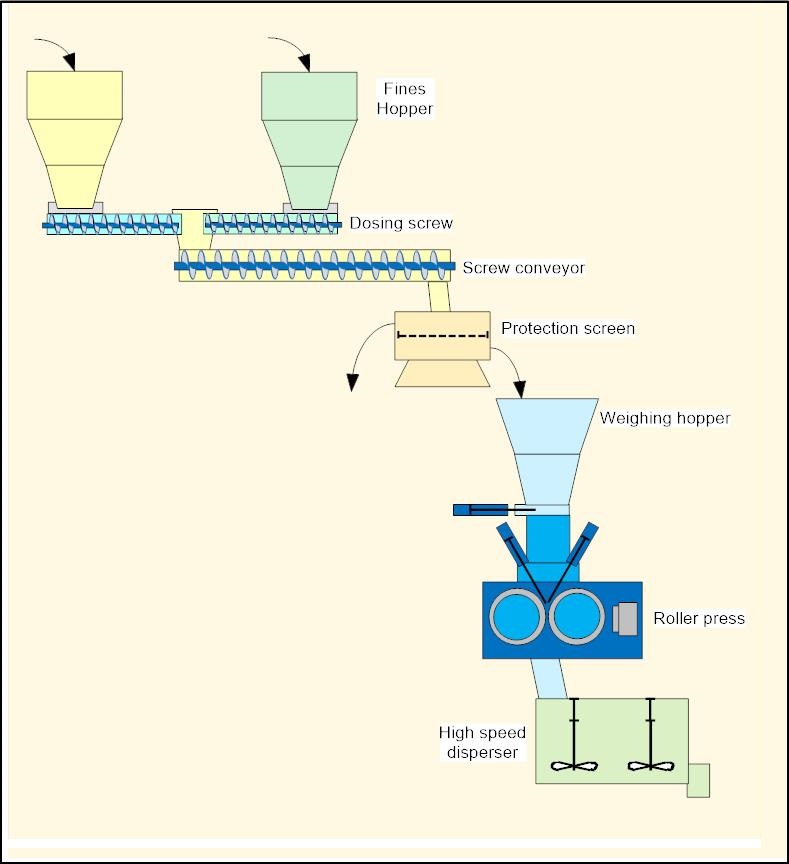
TIO2 GRINDING PROCESS
WITH ROLLER PRESS
AND BALL MILL
TIO2 GRINDING PROCESS
WITH ROLLER PRESS
AND HIGH SPEED DISPERSER
This grinding technology of Titanium Dioxide is based on the association of two successive grinding
steps:
- A high‐pressure primary grinding realised by a Roller Press. This equipment allows to change the TiO2 particles agglomerated at the furnace output in crumbly flakes, until a temperature of 110°C, thanks to their passages between two cylinders under pressure turning in the opposite direction. The size range of these flakes, obtained at the roller press output, is in the range of 5 to 60 mm.
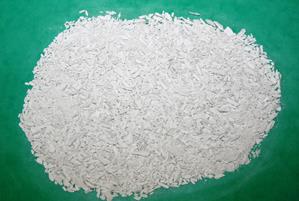
- A secondary grinding realised by a ball mill or a high‐speed disperser allowing the flake breaking shaped during the first step and the obtaining of a very fine product with a size range of about 0,2 to 3 µm. Beforehand this secondary grinding, the TiO2 flakes are mashed in the ball mill or the high‐speed disperser.
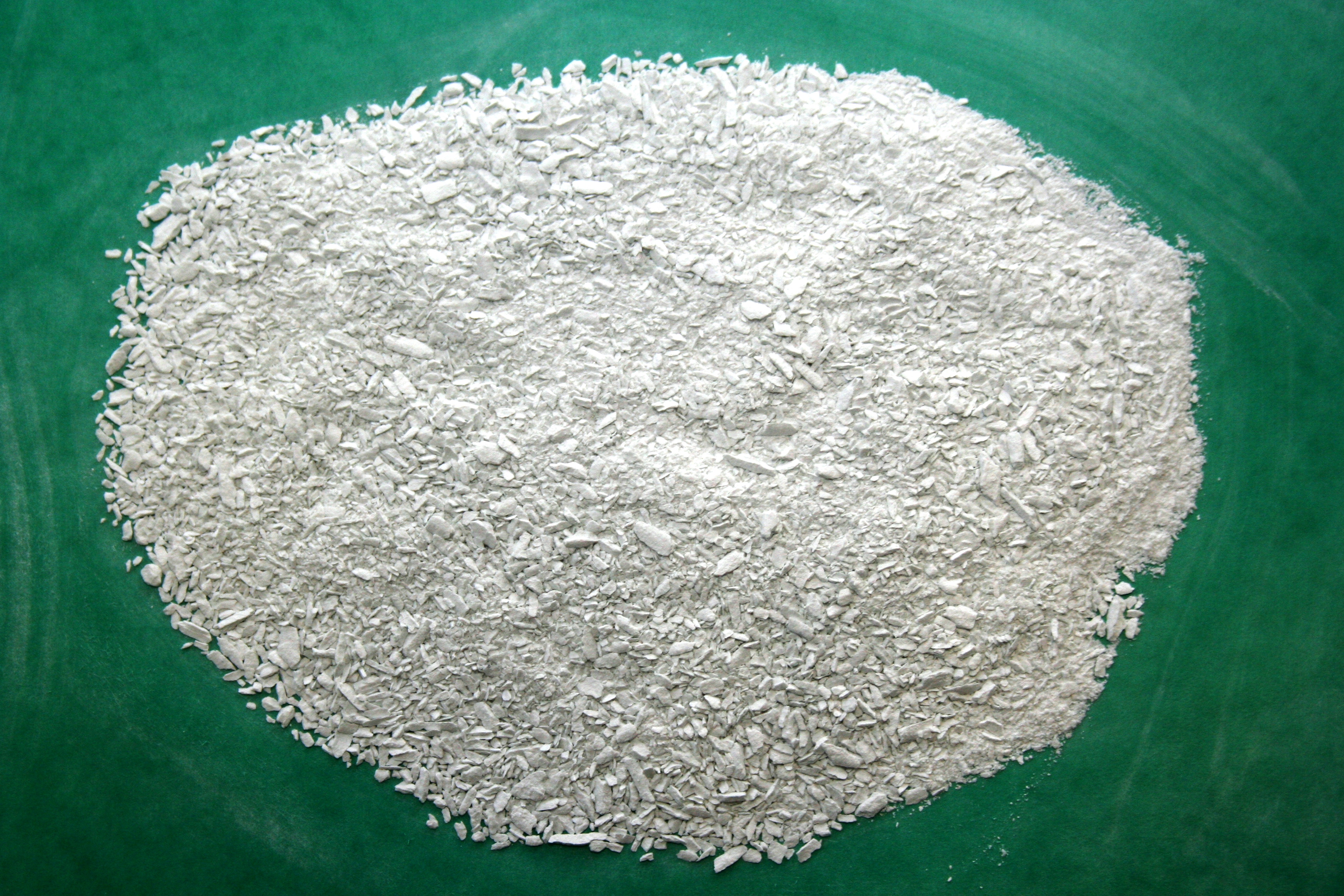
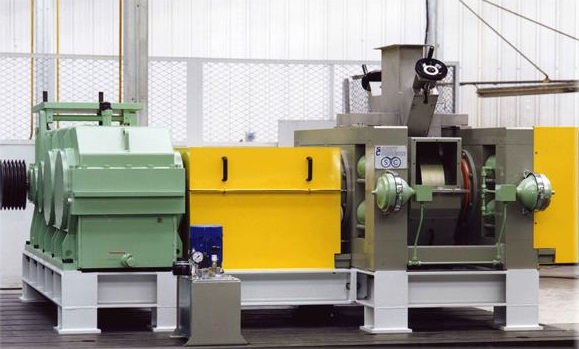
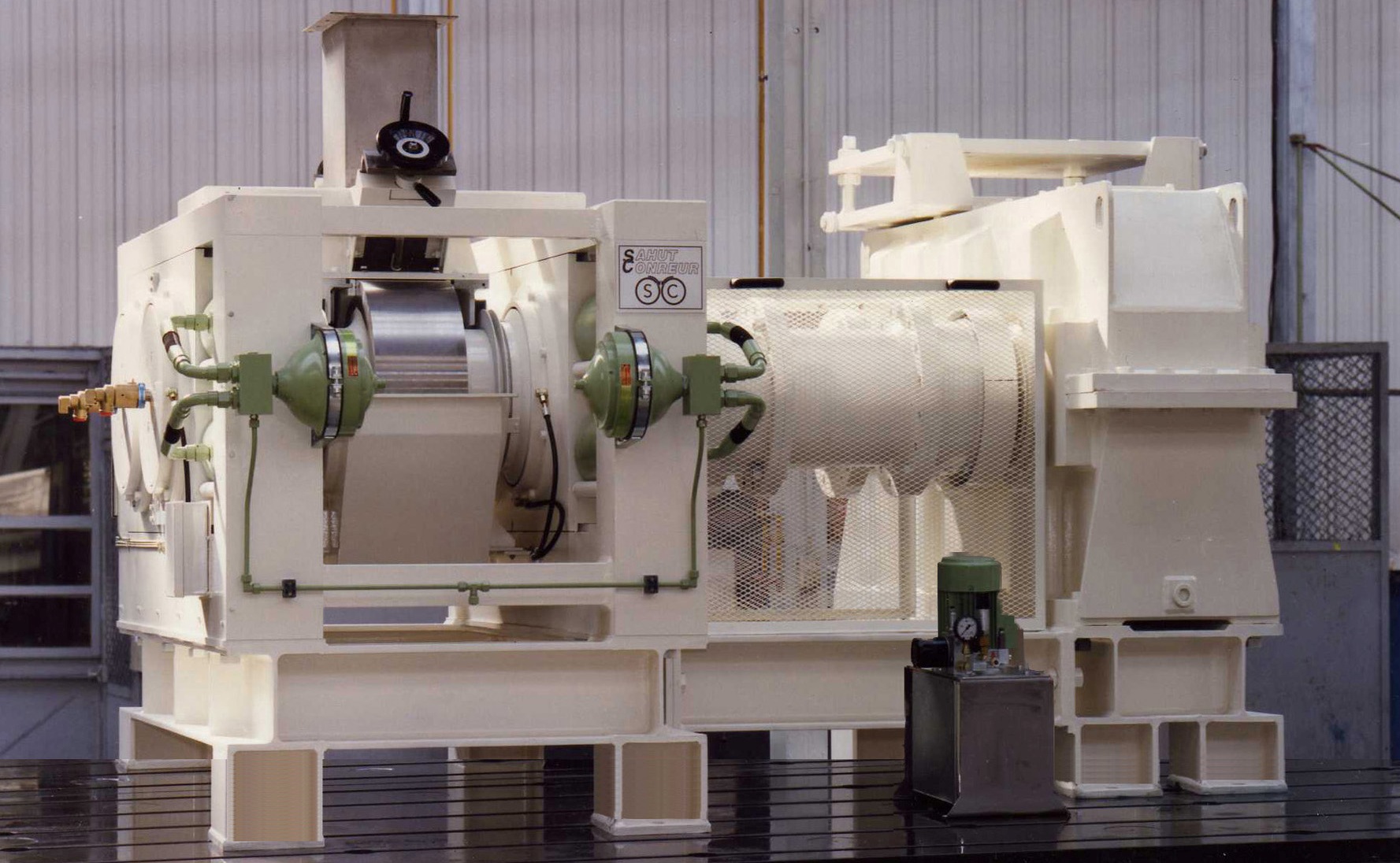
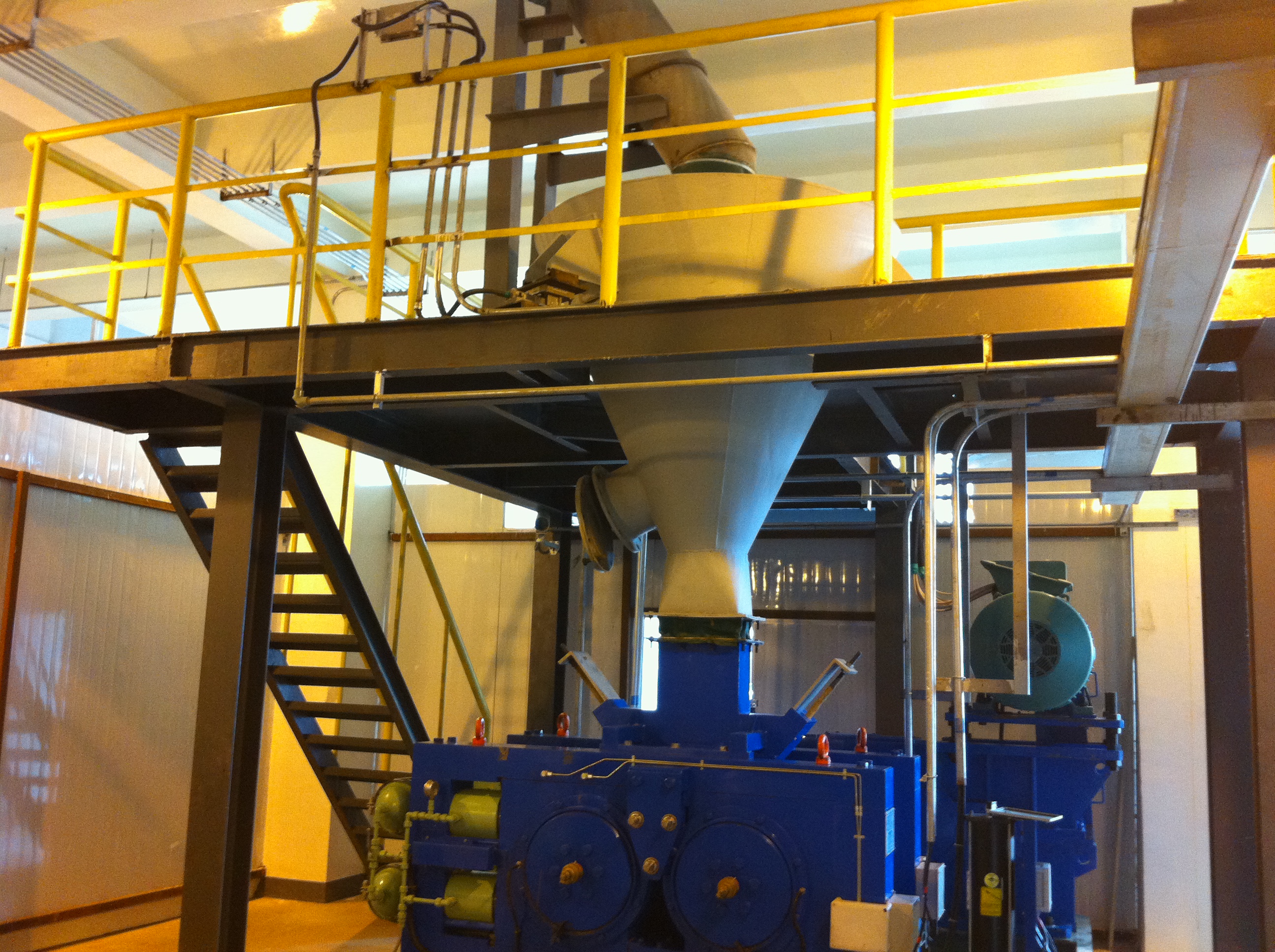
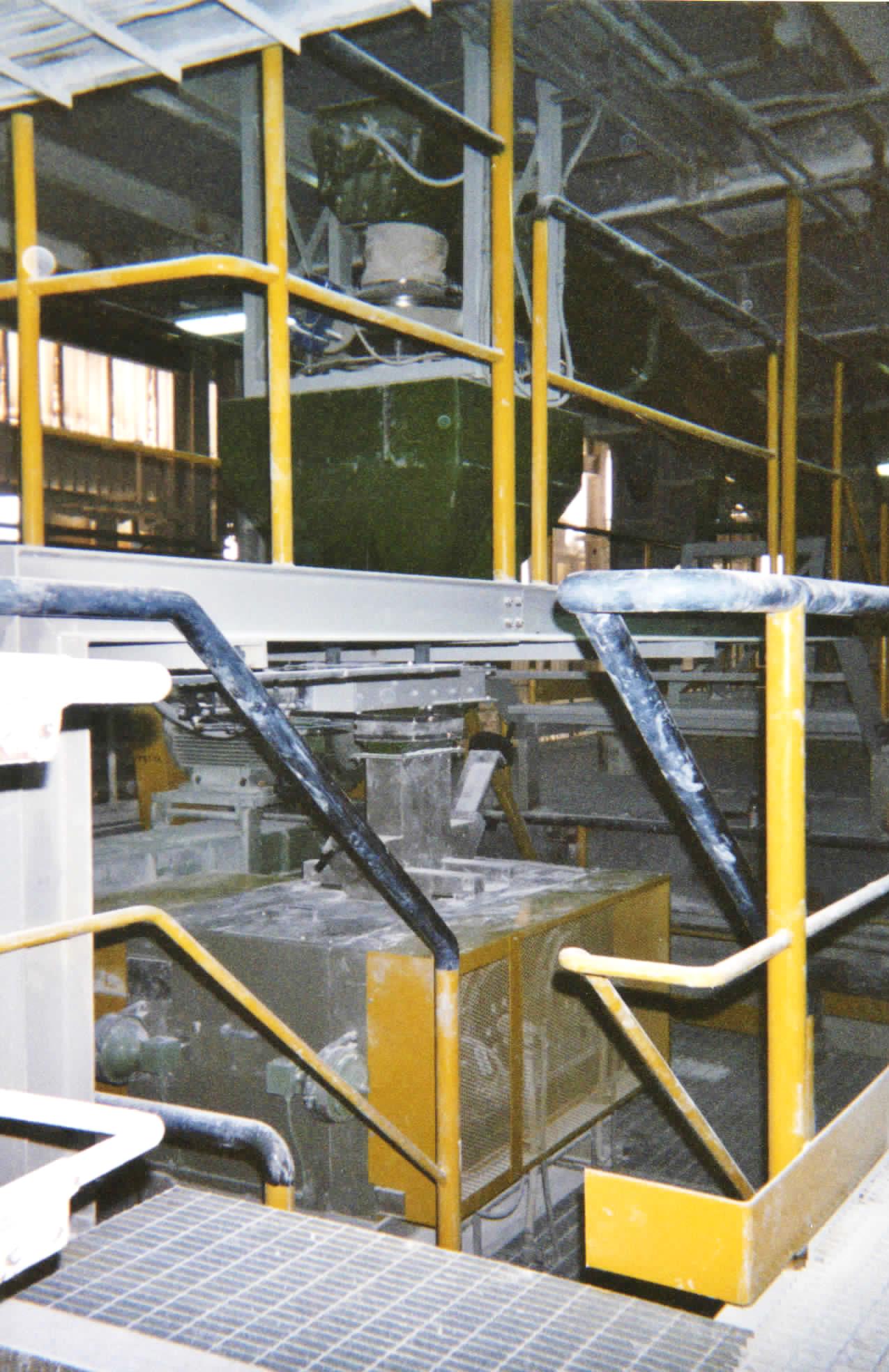
Roller press has increasingly highlighted its very important crushing effect in modern titanium
dioxide production
especially in the production of plastic grade TiO2 and Ink grade TiO2 such as TR52 products so on.
More and more
Titanium dioxide factories around the world especially sulfate titanium dioxide factories choose
roller press as their
important crushing equipment to improve the quality and stability of their products.
The below table shows the advantages generated by the introduction of grinding by Roller Press associate to high speed disperser instead of Raymond/Hammer‐mill.
The below table shows the advantages generated by the introduction of grinding by Roller Press associate to high speed disperser instead of Raymond/Hammer‐mill.
Raymond/Hammer-Mill | Roller Press with high speed disperser |
|
---|---|---|
Capacity (t/h) | 4 - 5 | 8 |
Noise (dB) | 120 | 80 |
Electric consumption (kWh/t) | 52 | 25 |
Annual capacity (t) | 20.000 | 50.000 |
Maintenance hours | – | 4 to 5 times less |
Typical flowsheets for cement grinding plants
SAHUT‐CONREUR
has developed roller presses, specially designed for the grinding of clinker for cement production. In the past, the grinding of clinker, commonly carried out by ball mills, required heavy investments and generated a high energy consumption associated with important maintenance costs.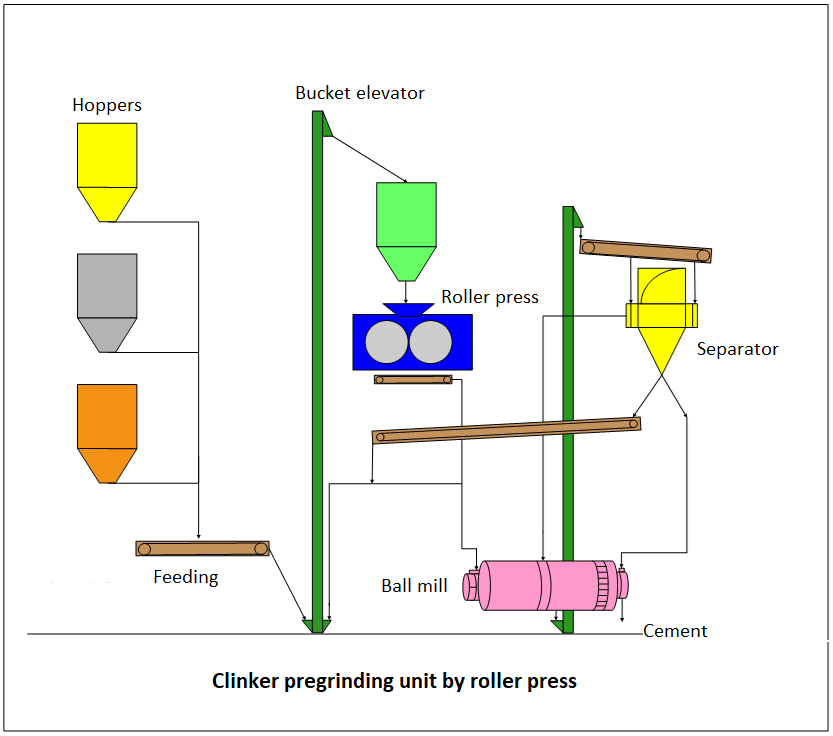
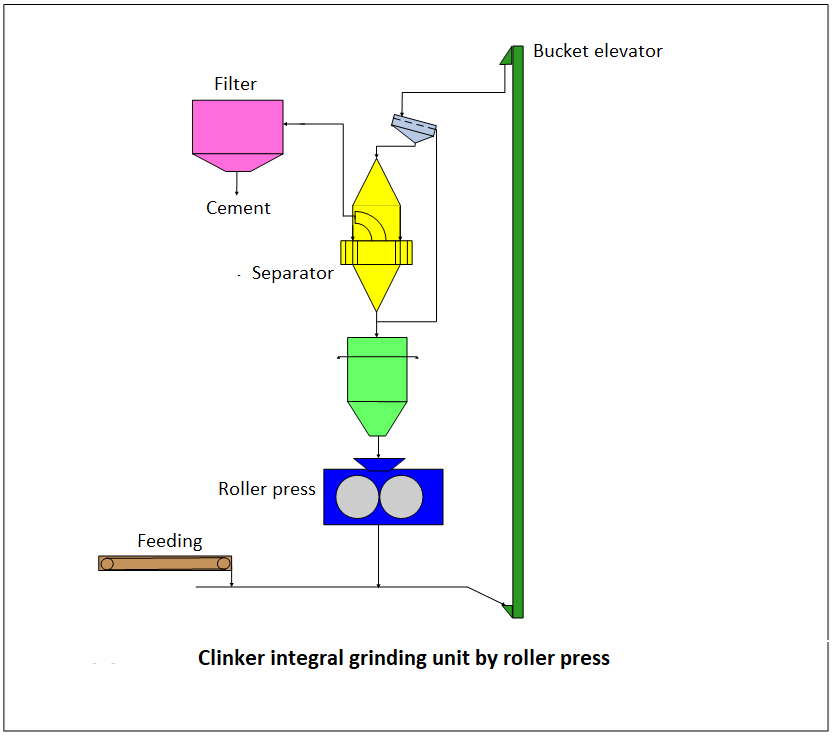
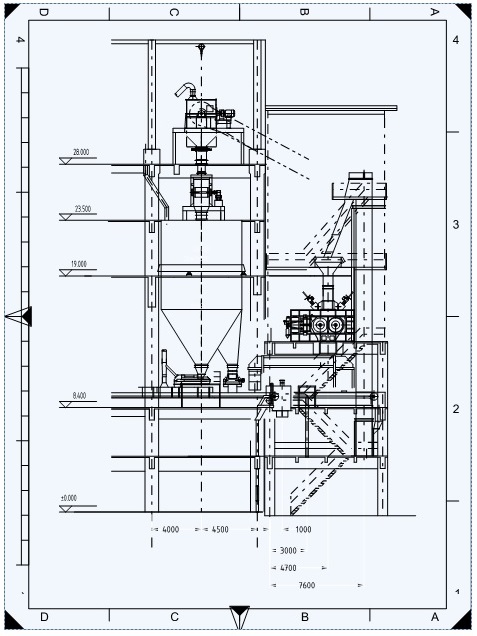
The Clinker grinding technology by roller press can be integrated in two configurations:
- In combination with a ball mill, the roller press performs a pre‐grinding of the clinker before it is fed into the ball mill.
- Integral grinding carried out by the combination of a roller press, a separator with desagglomerator stage and an elevator.
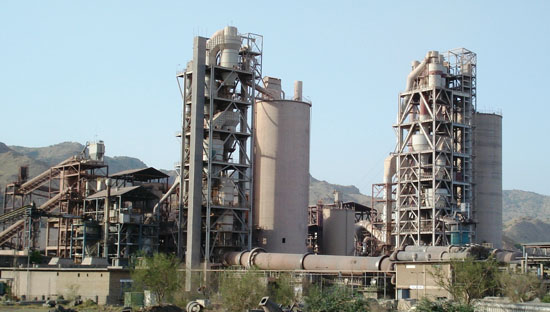
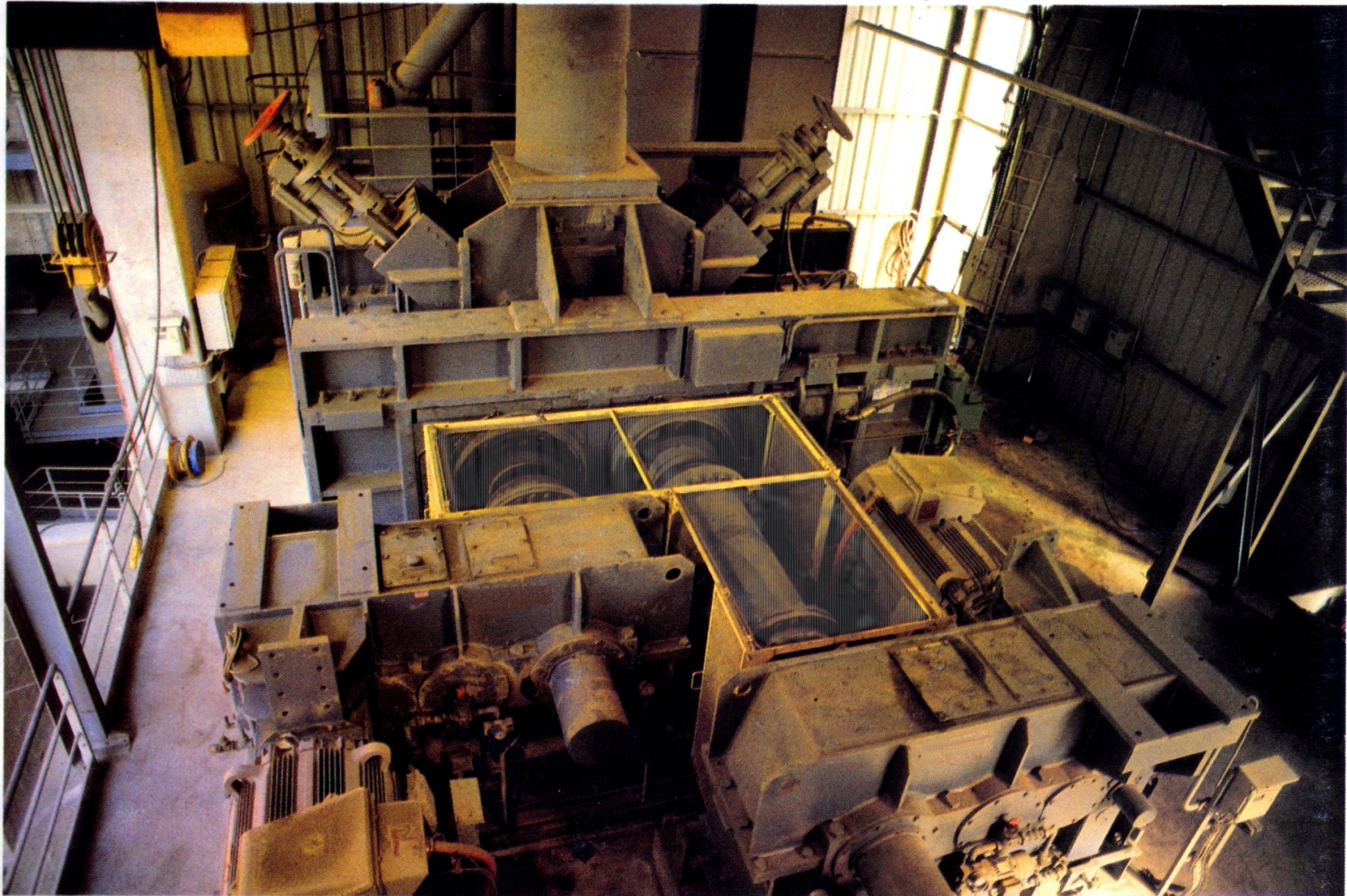
The below table shows the advantages generated by the introduction of a roller press in a clinker
grinding process
compared with a ball mill alone.
Ball Mill | Roller Press and ball mill |
|
---|---|---|
Capacity (t/h) | 35 | 83 |
Electric consumption (kWh/t) | 35 | 24 |
Electric consumption (kWh/t) Roller press |
- | 9 |
Maintenance hours | – | 4 to 5 times less |
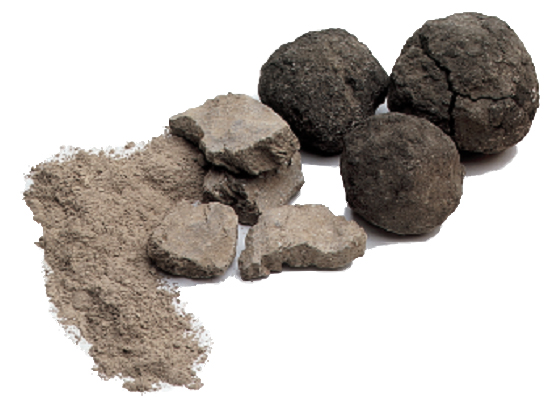