Compaction-Granulation equipment
The range of crushing/granulation equipment developed by
SAHUT-CONREUR
is specially adapted to the requirements of the compaction-granulation processes. These equipment are selected according to the physical properties of the material (hardness, abrasiveness,…), the final product final size range and the granules shape required for the marketable product. The yield of a compaction-granulation unit (ratio of the granules quantity per flakes quantity produced by the compactor) is essential in the selection and the combination of the adequate crushing-granulation equipment: from the compacted flakes, the maximum amount of granules of the calibrated size has to be produced while keeping as minimum the amount of fines generated; these fines will be recycled back to the compactor.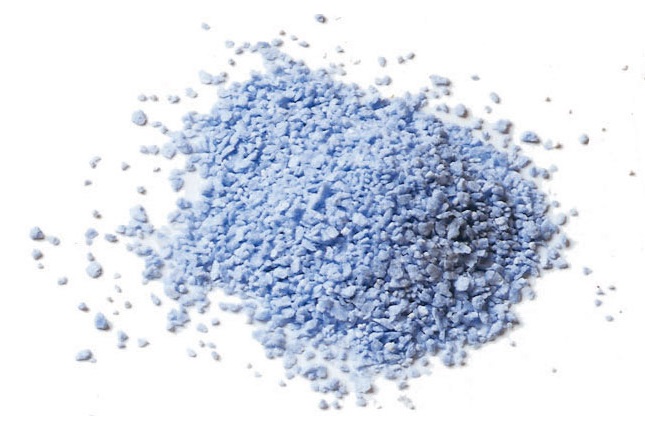
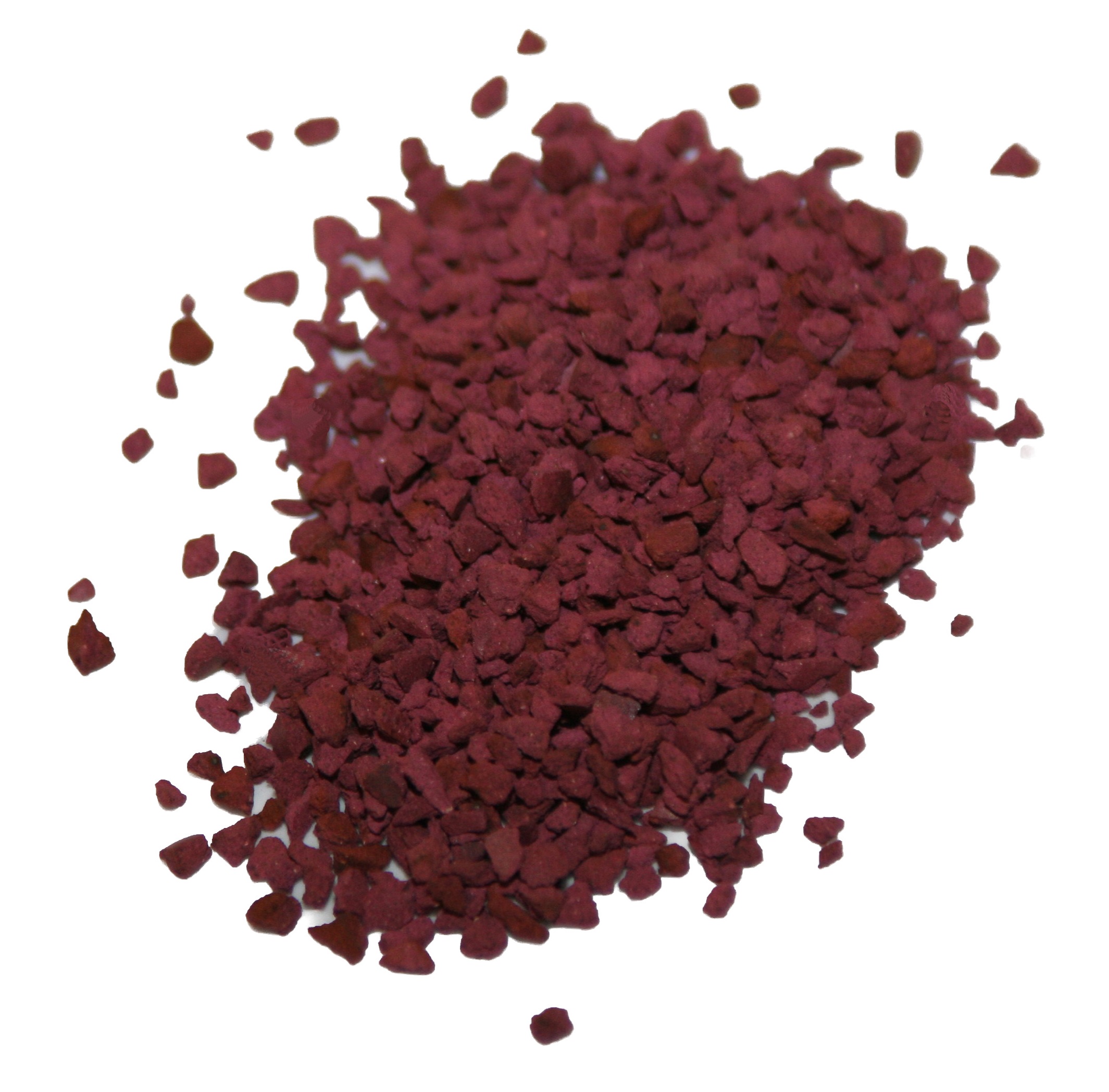
SAHUT-CONREUR
proposes 7 types of granulators/crushers:The flake-breaker
It consists of two rotors fitted with toothed discs rotating at the same speed and in reverse
direction: the flakes produced by the compactor run through the toothed discs and are reduced in
size. This equipment is usually placed between the compactor and the granulator/crusher in order to
reduce the flake size and so facilitate granulation.
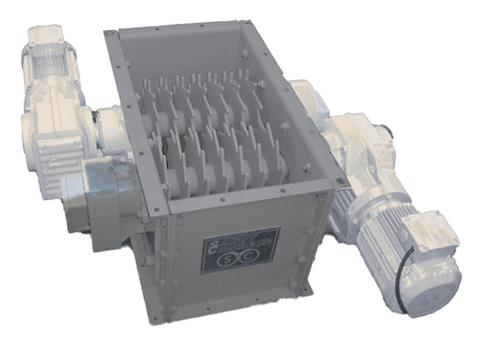
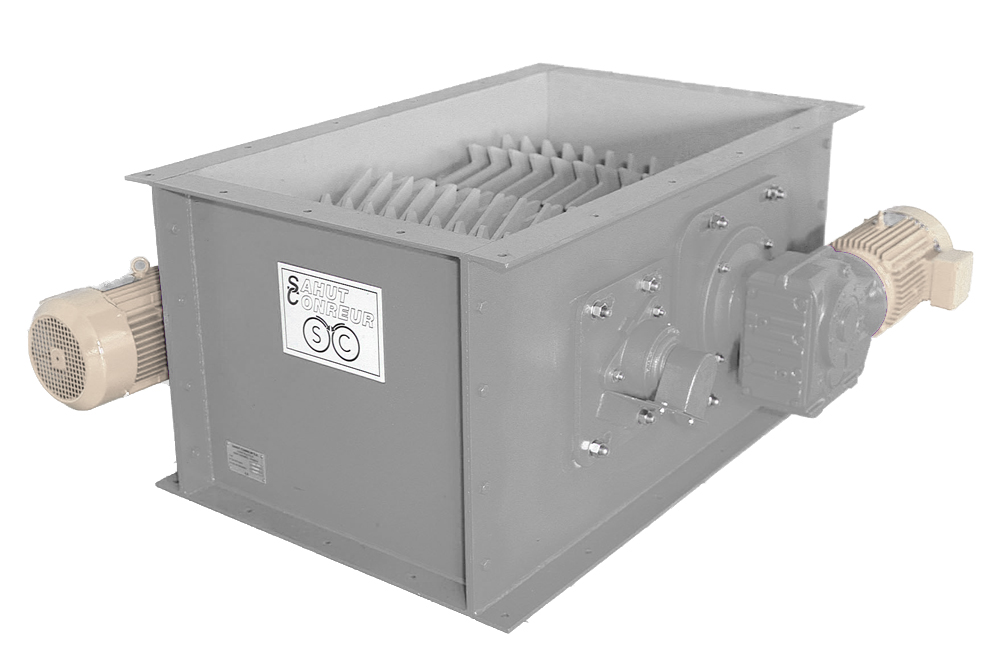
Type | Output(t/h) | Speed (Rpm) | Power (kW) | Rotor diameter (mm) | Rotor width (mm) | Weight (kg) |
---|---|---|---|---|---|---|
FB/30/20 | 0,1 - 1 | 25 | 2 x 1,5 | 200 | 200 | 300 |
FB/30/30 | 1 - 3 | 30 | 2 x 2.2 | 300 | 300 | 360 |
FB/30/40 | 3 - 10 | 40 | 2 x 3 | 300 | 400 | 400 |
FB/30/50 | 5 - 15 | 50 | 2 x 4 | 300 | 500 | 450 |
FB/40/50 | 6 - 17 | 50 | 2 x 4 | 400 | 500 | 500 |
FB/40/60 | 7 - 20 | 50 | 2 x 5.5 | 400 | 600 | 650 |
FB/40/90 | 10 - 25 | 50 | 2 x 7.5 | 400 | 900 | 850 |
FB/50/70 | 15 - 40 | 50 | 2 x 7.5 | 500 | 700 | 850 |
FB/50/90 | 20 - 55 | 50 | 2 x 9 | 500 | 900 | 1200 |
FB/50/95 | 25 - 60 | 50 | 2 x 9 | 500 | 950 | 1350 |
FB/50/110 | 30 - 70 | 50 | 2 x 11 | 500 | 1100 | 1450 |
FB/50/135 | 40 - 110 | 50 | 2 x 15 | 500 | 1350 | 2500 |
Options
Our flake-breaker can be customized following the below options:- Stainless steel 304L / 316L material construction
- Casing in special anti-wear material or with wear-plates
The hammer-mill
It consists of a rotor fitted with mobile hammers and a screen installed under the rotor; the rotor
speed and screen hole size are determined by the product to process and the end size range required.
The hammer-mill granulator can be installed as primary or secondary granulator.
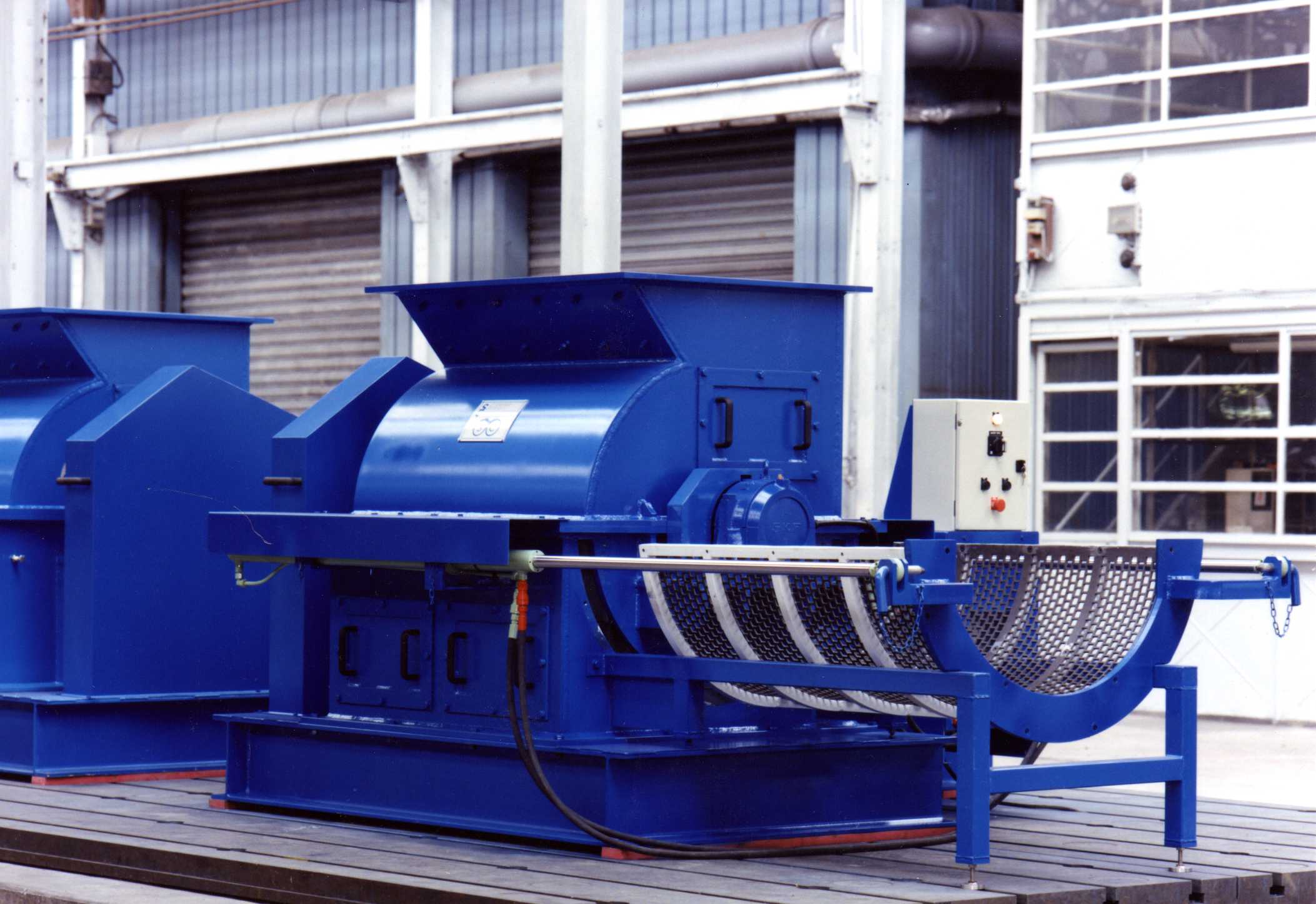
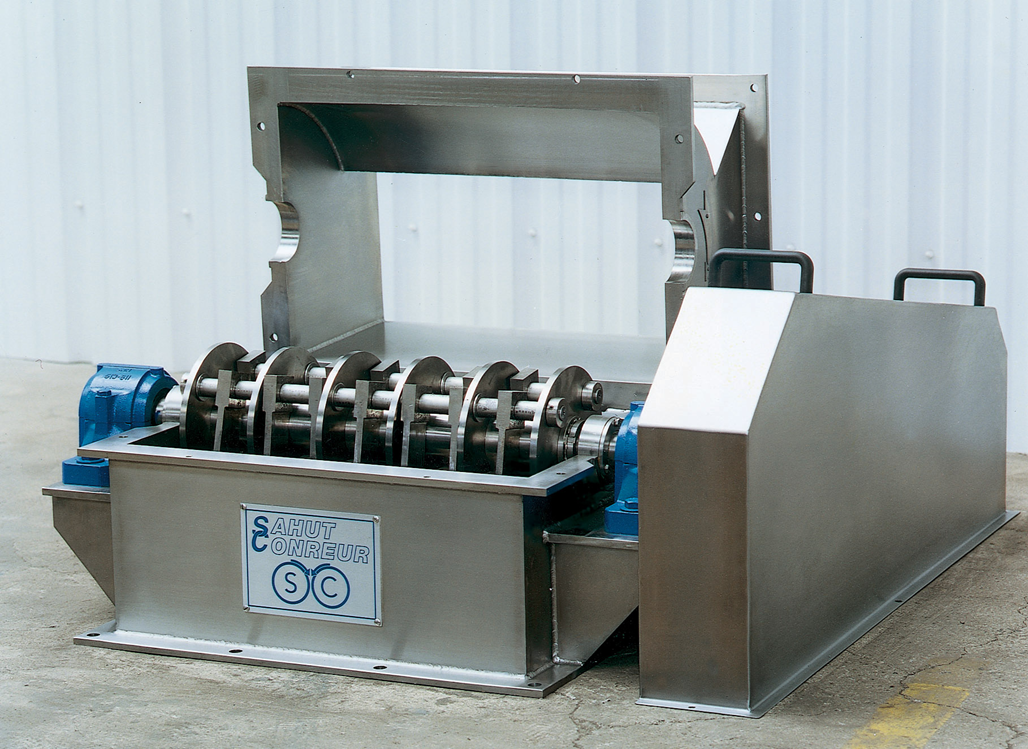
Type | Output(t/h) | Speed (Rpm) | Power (kW) | Weight (kg) |
---|---|---|---|---|
HM/30/20 | 0,3 - 1 | 1000 | 3 | 195 |
HM/40/30 | 1 - 3 | 800 | 7.5 | 250 |
HM/40/60 | 3 - 6 | 650 | 15 | 350 |
HM/50/70 | 6-30 | 650 | 30 | 800 |
HM/55/90 | 10-50 | 650 | 37 | 1000 |
HM/70/100 | 15 - 70 | 650 | 45 | 2500 |
HM/90/100 | 20 - 90 | 650 | 55 | 3500 |
HM/90/120 | 25 - 100 | 650 | 75 | 4200 |
Options
Our hammer-mill can be customized following the below options:- Stainless steel 304L / 316L material construction
- Casing in special anti-wear material or with wear-plates
The single-deck grid granulator
It is equipped with a rotor fitted with several blades and a perforated grid is placed under the
rotor ; the rotor rotating at low speed forces the product through the perforations. Thanks to this
grinding technique, the granules have a rounder shape. Besides, the crushing/ granulation yield is
higher than the one obtained with the hammer-mill. The single-deck grid granulator will be installed
as primary or secondary granulator.
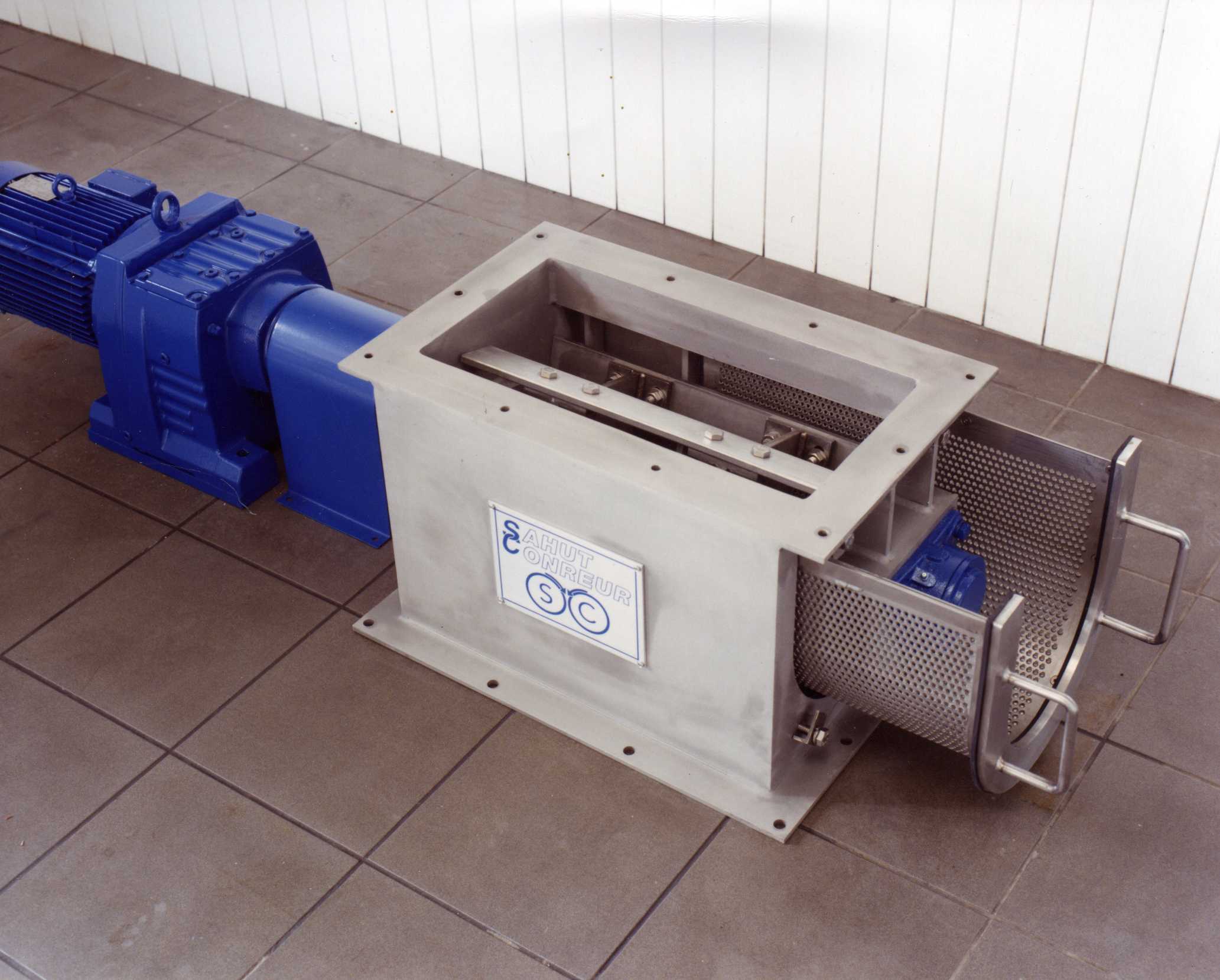
Type | Output(t/h) | Speed (Rpm) | Power (kW) | Rotor diameter (mm) | Rotor width (mm) | Weight (kg) |
---|---|---|---|---|---|---|
SG 6 | 0,1 - 0,5 | 0 - 150 | 0,55 | 100 | 60 | 100 |
SG 10 | 0,5 - 1,5 | 0 - 150 | 1.5 | 200 | 100 | 135 |
SG 20 | 1 - 2 | 50 - 250 | 3 | 300 | 400 | 175 |
SG 25 | 1 - 3 | 50 - 250 | 5.5 | 300 | 500 | 300 |
SG 50 | 1 - 4 | 50 - 250 | 7.5 | 430 | 750 | 500 |
SG 100 | 2 - 10 | 50 - 250 | 15 | 600 | 1000 | 1000 |
Options
Our single-deck grid granulator can be customized following the below options:- Stainless steel 304L / 316L material construction
- Casing in special anti-wear material or with wear-plates
The double-deck grid granulator
It includes a primary granulator and two secondary granulators. Taking the throughput of the grid of
the secondary granulator into account, the flow of product from the primary granulator is
distributed among both secondary granulators mounted in parallel. The aperture of the grid of the
secondary granulators can correspond to the upper size requested for the marketable granules: in
that case, the upper cloth can be removed and the circulating load in the handling equipment
reduced.
Type | Output (t/h) | Speed (Rpm) | Power (kW) | Rotor diameter (mm) | Rotor width (mm) | Weight (kg) |
---|---|---|---|---|---|---|
DG 50 | 5 - 10 | 30 | 18.75 | 500 | 500 | 2000 |
DG 100 | 10 - 20 | 35 | 56.25 | 730 | 875 | 3500 |
DGI 200 | 20 - 40 | 35 | 90.75 | 730 | 1750 | 7000 |
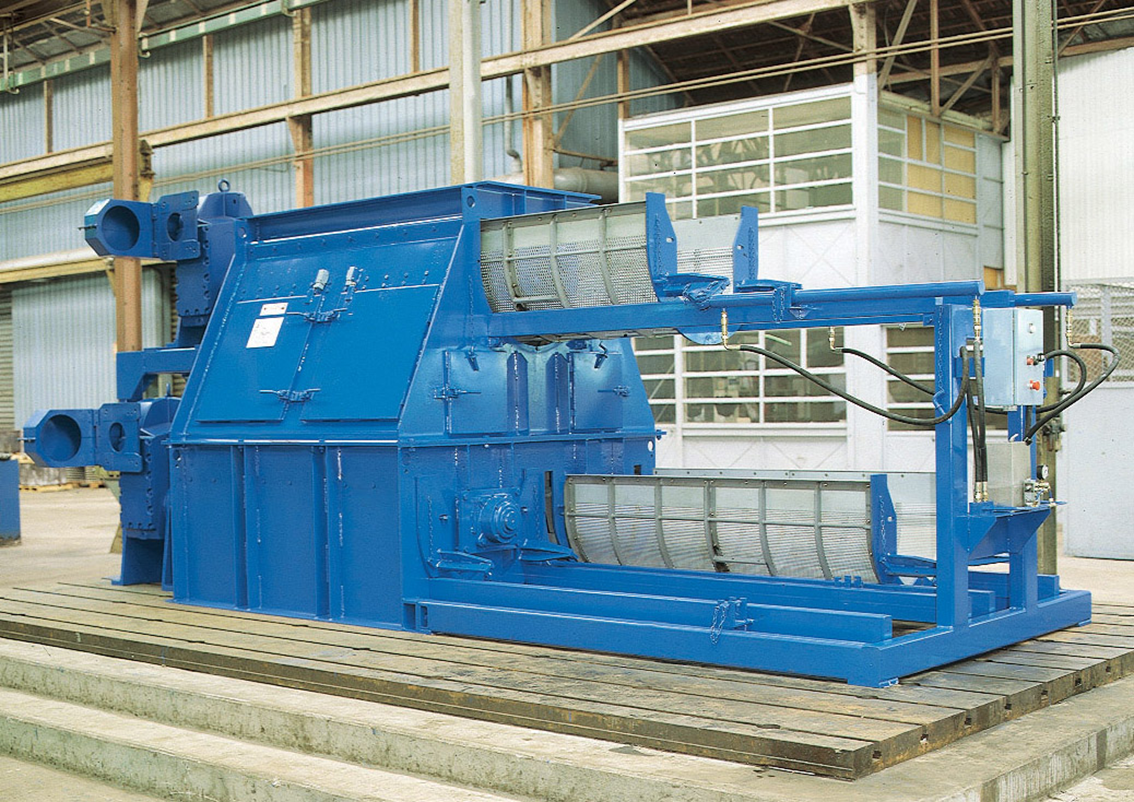
Options
Our double-deck granulator can be customized following the below options:- Stainless steel 304L / 316L material construction
- Casing in special anti-wear material or with wear-plates
The oscillating or continuous rotor granulator
The granulator is equipped with a rotor fitted with several arms; the product is crushed when
running through the screen installed under the rotor. This equipment is particularly adapted for
producing a fine particle size range in small throughput plants.
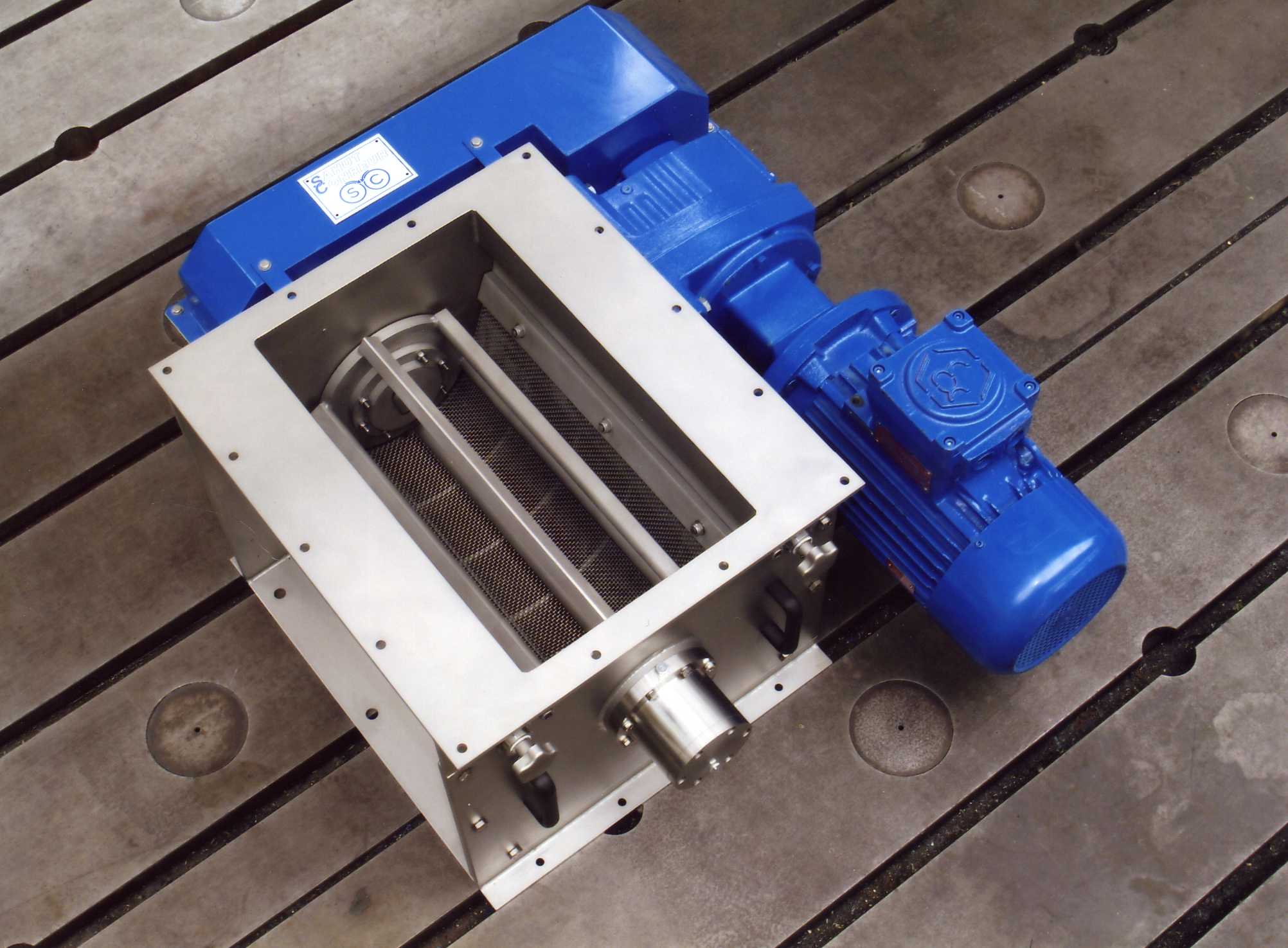
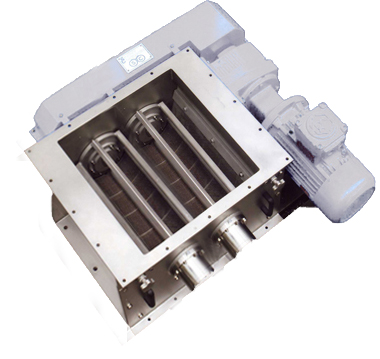
Type | Output(t/h) | Speed (Rpm) | Power (kW) | Rotor diameter (mm) | Rotor width (mm) | Weight (kg) |
---|---|---|---|---|---|---|
SC 60 | 0,1 - 0,2 | 0 - 150 | 0,55 | 100 | 60 | 40 |
SC 100 | 0,2 – 0.25 | 0 - 150 | 1.1 | 100 | 100 | 80 |
SC 200 | 0.25 - 0.5 | 0 - 250 | 1,5 | 140 | 220 | 150 |
SC 400 | 0.5 – 0.75 | 0 - 250 | 3 | 180 | 390 | 230 |
SC 500 | 0.75 - 1 | 0 - 250 | 5.5 | 220 | 480 | 325 |
SC 600 | 1 - 2 | 0 - 250 | 7.25 | 280 | 600 | 400 |
SAHUT-CONREUR
also offers the supply of integrated compact units including crushing - granulation systems. These systems can be adapted in existing equipment or units according to the needs and production requirements.Options
Our oscillating or continuous rotor granulator can be customized following the below options:- Stainless steel 304L / 316L material construction
- Casing in special anti-wear material or with wear-plates
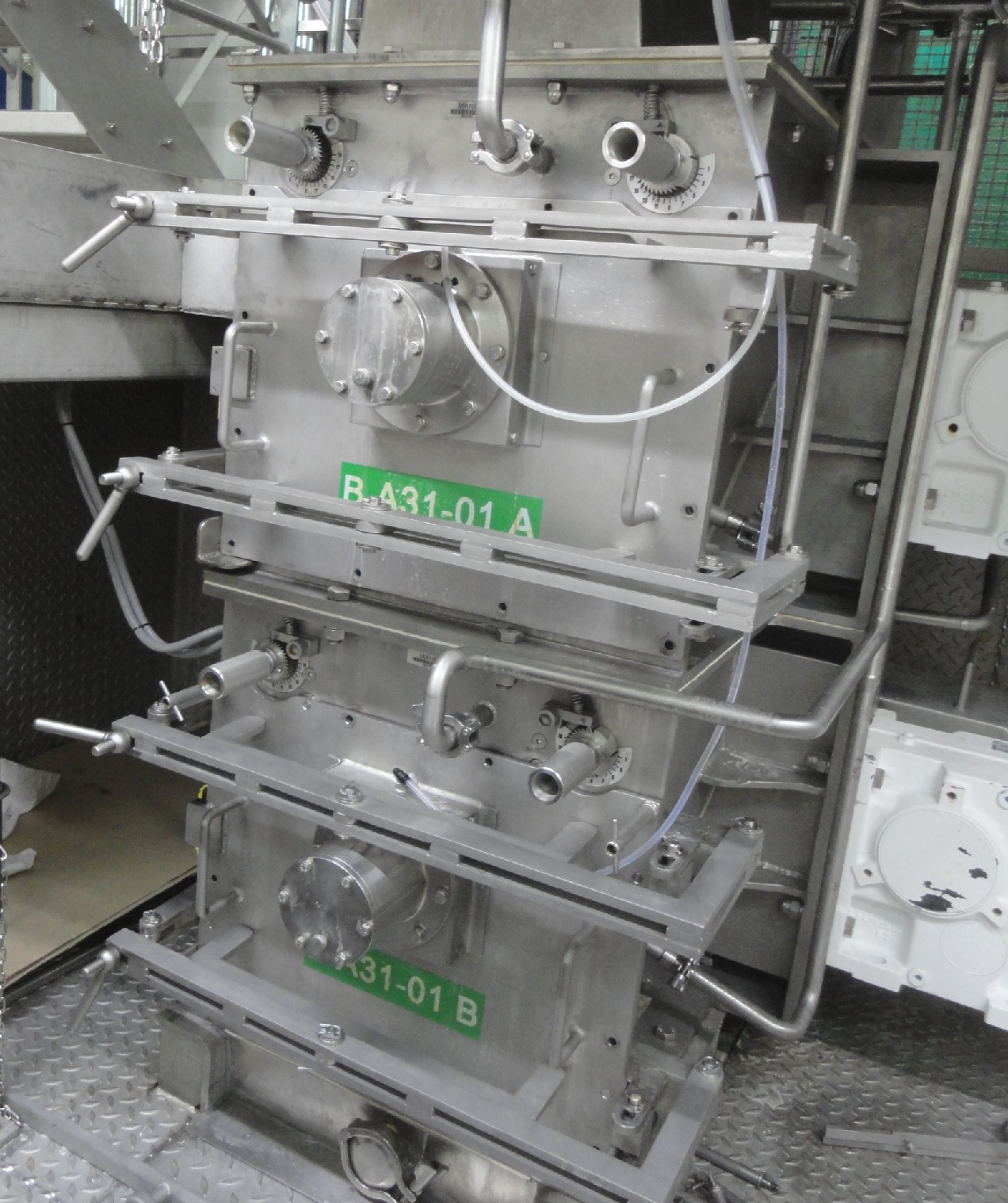
The knife crusher
It consists of two rotors, the working surface of which is machined to obtain either vertical knives
or horizontal knives. The product running through the rotors is crushed by the knives. The size
range of the crushed material (between 2 and 20 mm) is conditioned by the gap between rotors and the
distance between knives.
Type | Output (t/h) | Power (kW) | Rotor diameter (mm) | Rotor width (mm) | Weight (kg) |
---|---|---|---|---|---|
KC/250/300 | 0,1 - 1 | 2.2 | 250 | 300 | 300 |
KC/250/600 | 1 - 3 | 5.5 | 250 | 600 | 600 |
KC/250/900 | 3 - 4 | 7.5 | 250 | 900 | 900 |
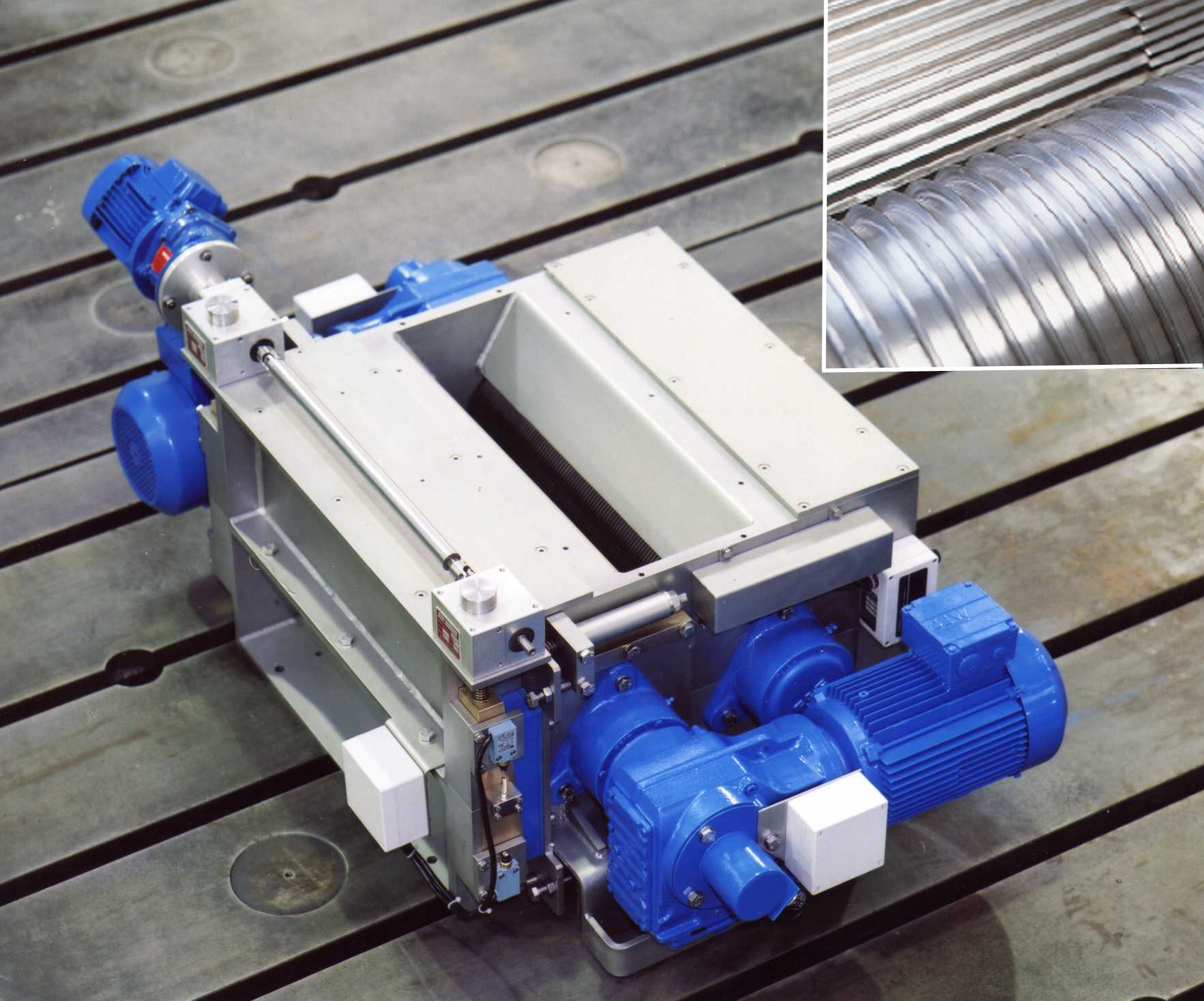
The smooth rolls crusher
It is well adapted for finer particle size range with an average diameter between 0.3 and 2 mm. With
this crusher, the size range can be perfectly targeted while reaching crushing yields vastly
superior to the usual yields for such a fine particle size range.
Type | Output (t/h) | Power (kW) | Rotor diameter (mm) | Rotor width (mm) | Weight (kg) |
---|---|---|---|---|---|
SRC/250/300 | 0,1 - 1 | 2.2 | 250 | 300 | 300 |
SRC/250/600 | 1 - 3 | 5.5 | 250 | 600 | 600 |
SRC/250/900 | 3 - 4 | 7.5 | 250 | 900 | 900 |
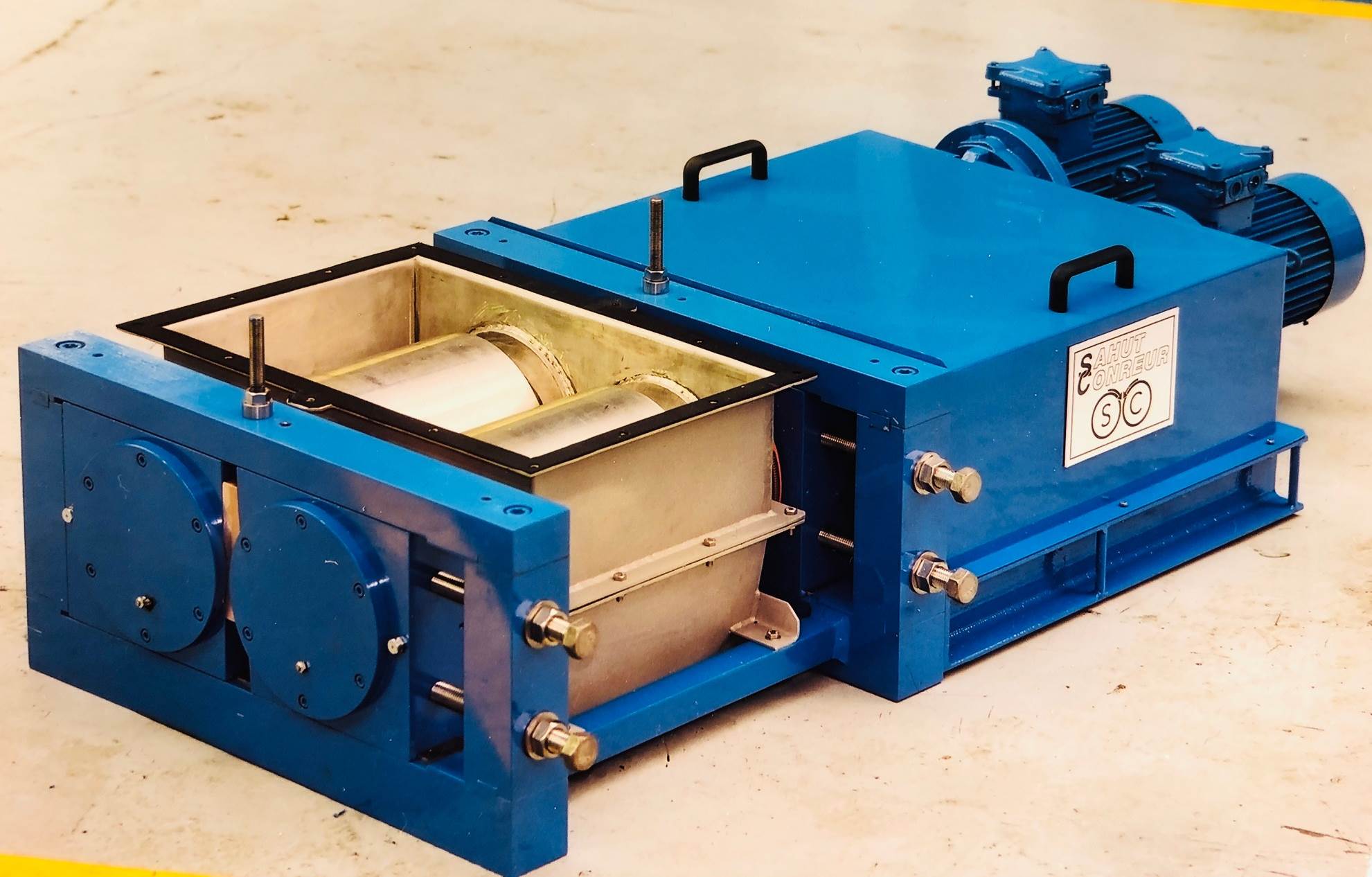
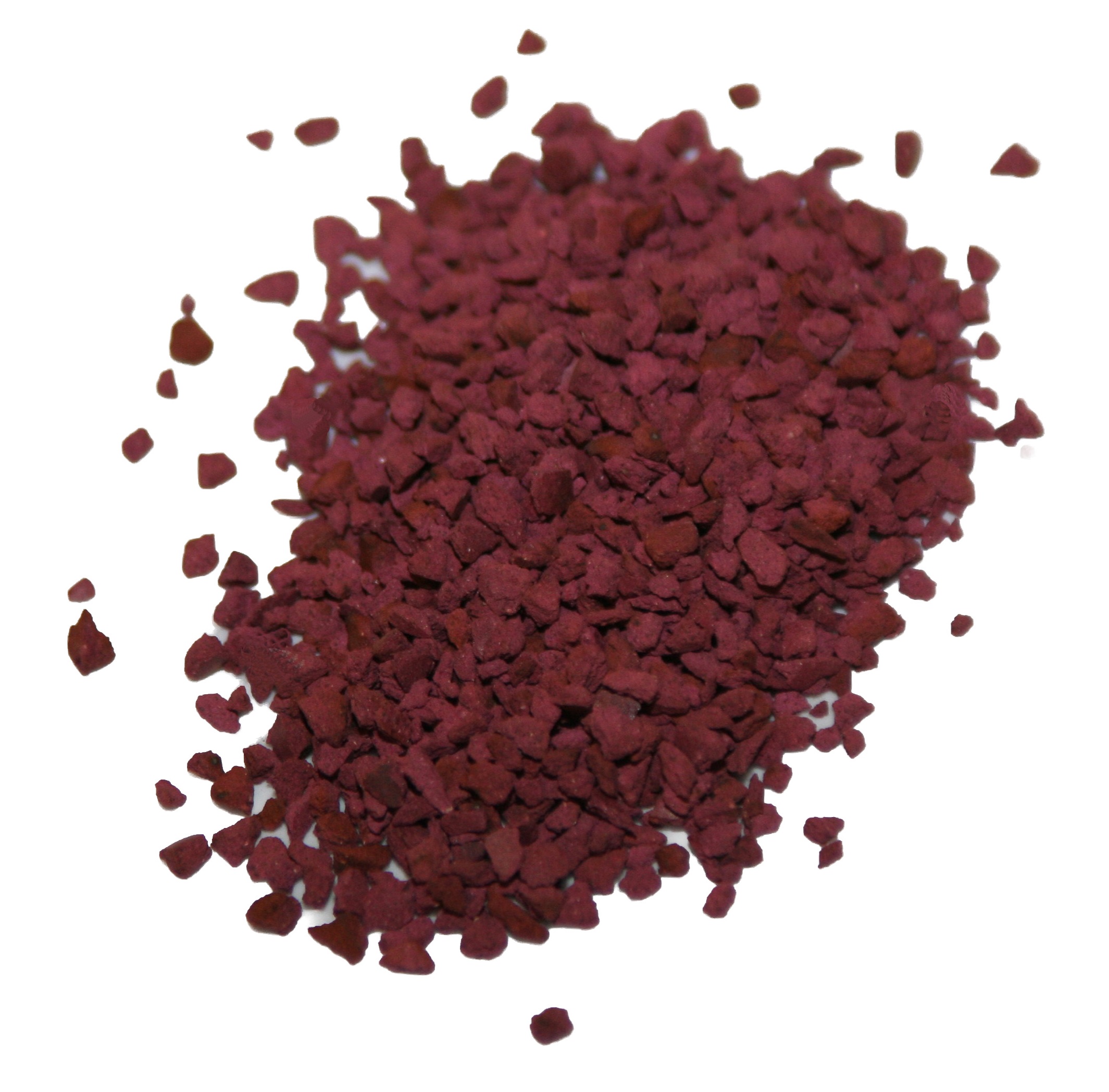
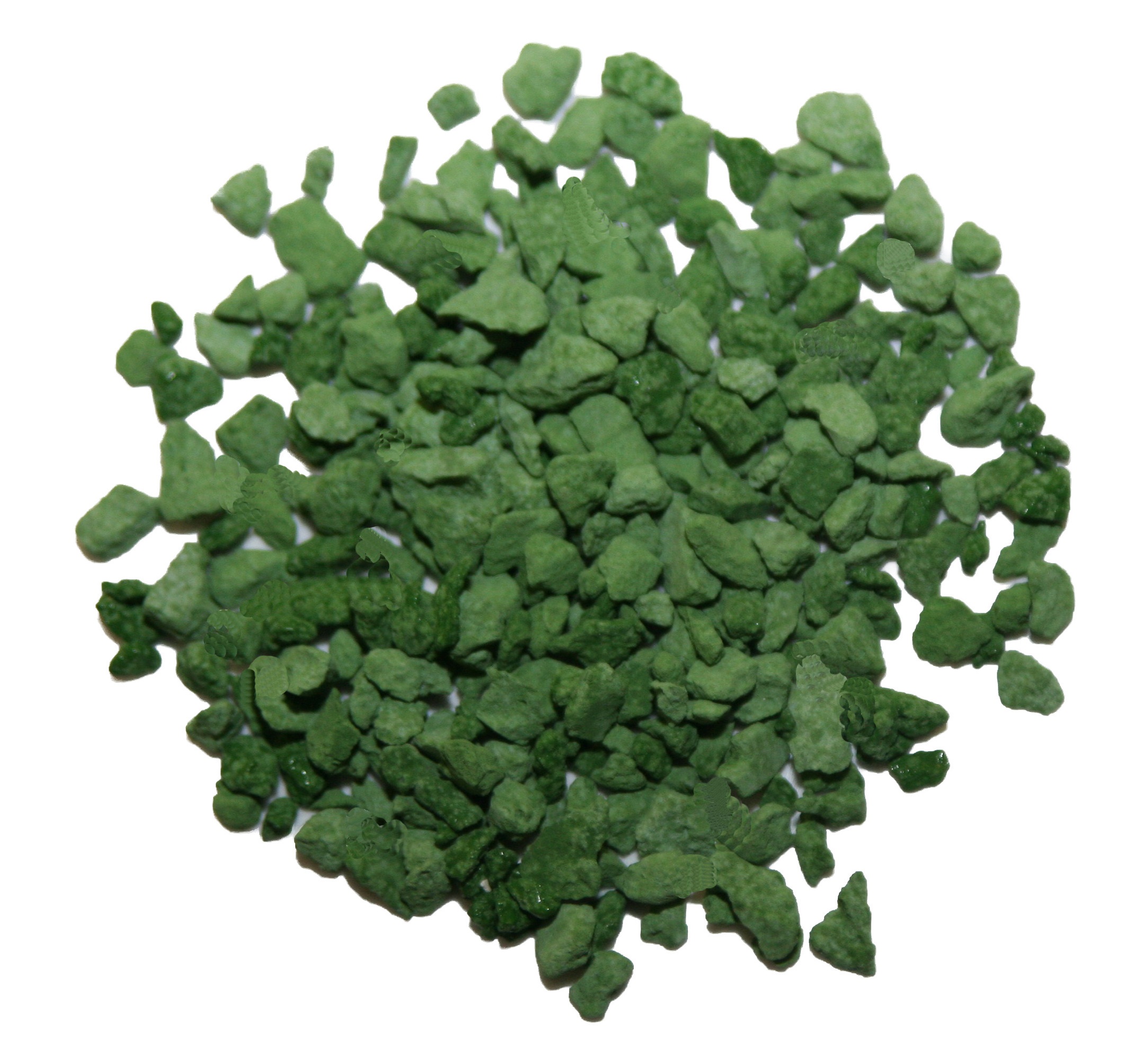
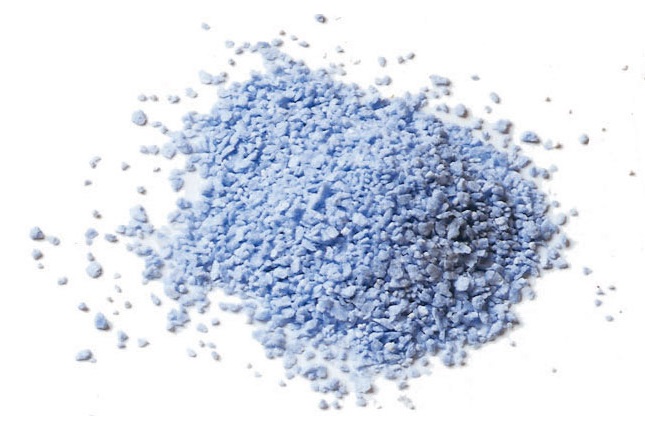
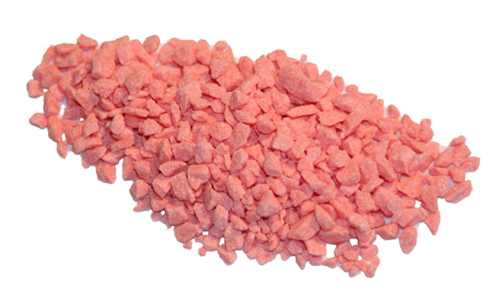