Hot Compacting iron
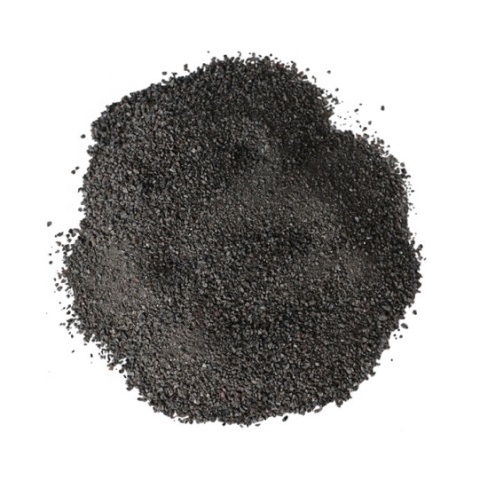
Thanks to the experience obtained from the 1970's in the hot briquetting of Waelz oxides (up to
650°C) and phosphate (up to 1050°C),
SAHUT-CONREUR
has introduced in the beginning of the 2000’s an innovating concept to the steelmaking industry for making the feed material into a densified form of lump. This process occurring at a high temperature (up to 850°C) and achieved by means of a compactor is called HCI (Hot Compacting Iron). Developed in tight collaboration with the South Korean steel-maker leading company Posco, the HCI process offers a true technological alternative to the common HBI (Hot Briquetting Iron) process.
The smelting reduction process of producing molten iron using ore and coal directly, is separated by
a reduction process for producing the direct reduction iron (DRI) and the melting process for
generating gas by the combustion of coal and melting the charged materials. In order for the
entire process to be continuously run in a stable state, it is necessary to add a process that
connects the separated two processes.
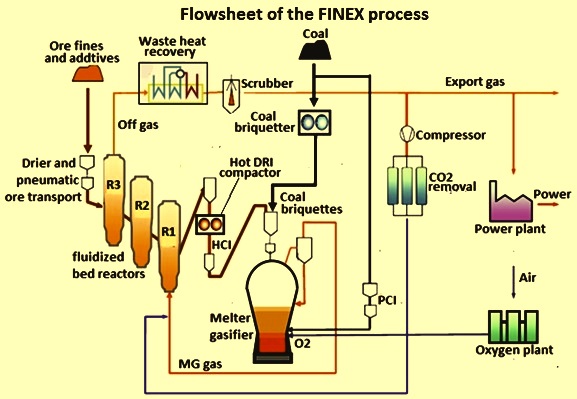
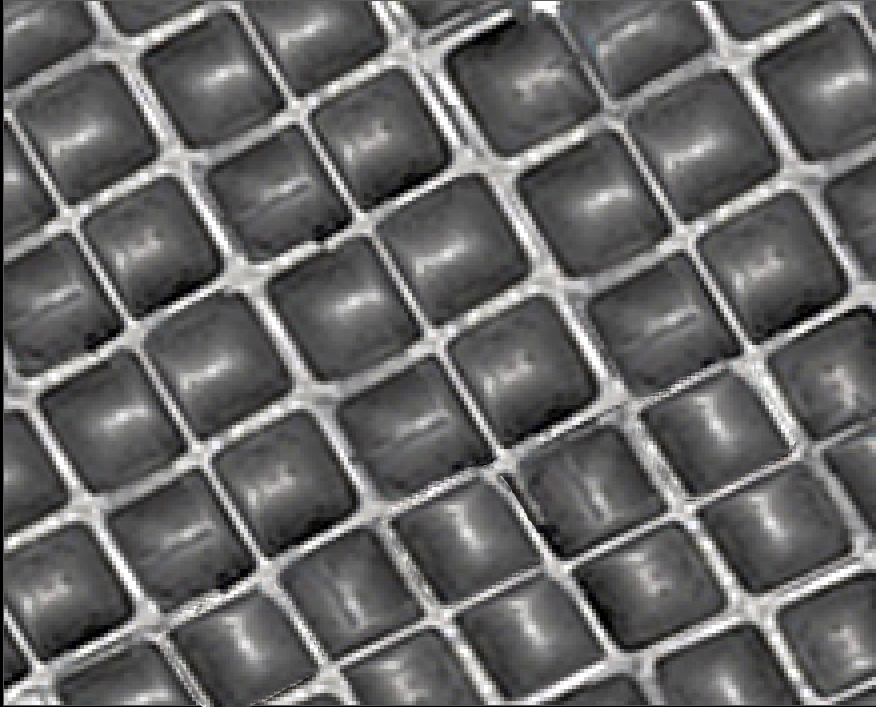
HCI process has been developed as a technology to connect Fluidized Bed reactor (FB) and
Melter-Gasifier (MG) to FINEX process, a smelting reduction process developed by POSCO. That is,
Fine DRI with the addition of additive is produced in the FB reactor, and this DRI is made in the
form of plate at a high temperature when passing in the HCI compactor to be then crushed to the
appropriate size for MG in an associated separator.
HCI process is very similar to HBI process in terms of the process of densifying the material at
high temperatures. However, the function of HCI is to connect the melting and reducing process so
that the entire process can be continuously run. Therefore, the impact of HCI's productivity and
facility reliability on the entire process is higher than that of HBI.
The application of commercialized HBI technology has been reviewed early in FINEX development but considering the material conditions required in the Iron making process, the HBI characteristics with high density and high metallization, low gangue content have been judged to be over-specification. For this reason, HCI technology has been developed as a new technology for the smelting reduction process and has been first applied to FINEX.
HCI process produces a densified form of DRI suitable for iron making process. As a result of its application to FINEX, it is able to reduce the number of machine installations due to its high productivity, which reduces investment costs and by the long service life of the compactor, it contributes to the improving of the overall process availability
The application of commercialized HBI technology has been reviewed early in FINEX development but considering the material conditions required in the Iron making process, the HBI characteristics with high density and high metallization, low gangue content have been judged to be over-specification. For this reason, HCI technology has been developed as a new technology for the smelting reduction process and has been first applied to FINEX.
HCI process produces a densified form of DRI suitable for iron making process. As a result of its application to FINEX, it is able to reduce the number of machine installations due to its high productivity, which reduces investment costs and by the long service life of the compactor, it contributes to the improving of the overall process availability
HCI process features
Productivity | Lifetime of roll (Days) | Width of roll (mm) | Force feeder Screw Type |
||
---|---|---|---|---|---|
Normal | Max | ||||
HCI | 55 - 60 | 85 | 500 | 600 - 700 | Double screw |
Scalability of HCI technology
The features of HCI can be summarized as follows:- Medium metallization and density, high gangue contents
- High productivity, long service life of equipment
- low investment cost and low production cost
The areas where HCI can be economically applied are as follows:
- Smelting reduction process
- Steel Waste Recycling process (Rotary Kiln, RHF, etc)
- HBI production for Blast furnace
- Agglomeration area at high temperatures with low cost, high productivity without restrictions on the use of raw materials
The HCI process takes place at high temperature, approx. 500-650°C, with a high compaction pressure
up to 120 kN/cmL. On the outlet of the compactor, the briquetted bands are conveyed to a separator
which separates the briquettes band into graps of individual/several briquettes.
The hot compactor is the key equipment of a Hot DRI compaction plant.
The hot compactor is the key equipment of a Hot DRI compaction plant.
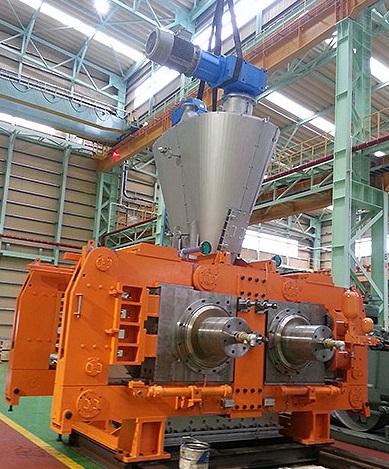
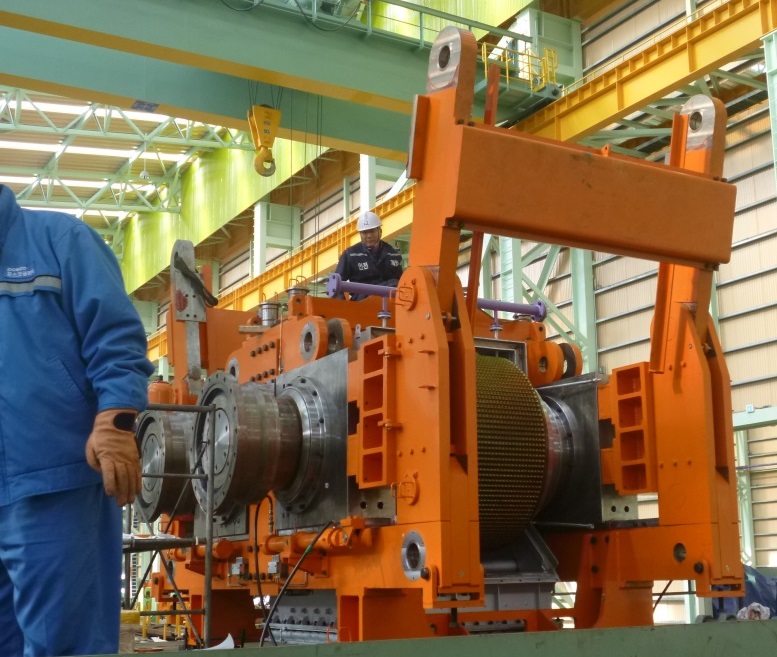
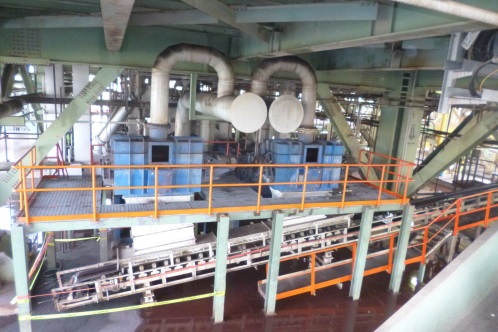
A quench cooler tank (static or vibratory design) is placed at the end of the HCI unit to collect
HCI produced in over quantity than requested by the process (injection into the melter gasifier) to
cool down the HCI briquettes under 80-100°C to store it for next usage.
Hereafter a typical flowsheet of a HCI unit with 8 lines (1 in stand-by) from the outlet of the
shaft furnace up to the cooled briquettes discharge outlet. This unit can reach for a net briquettes
capacity up to approx. 322 TPH (total annual capacity approx. 2.8 MTPY)
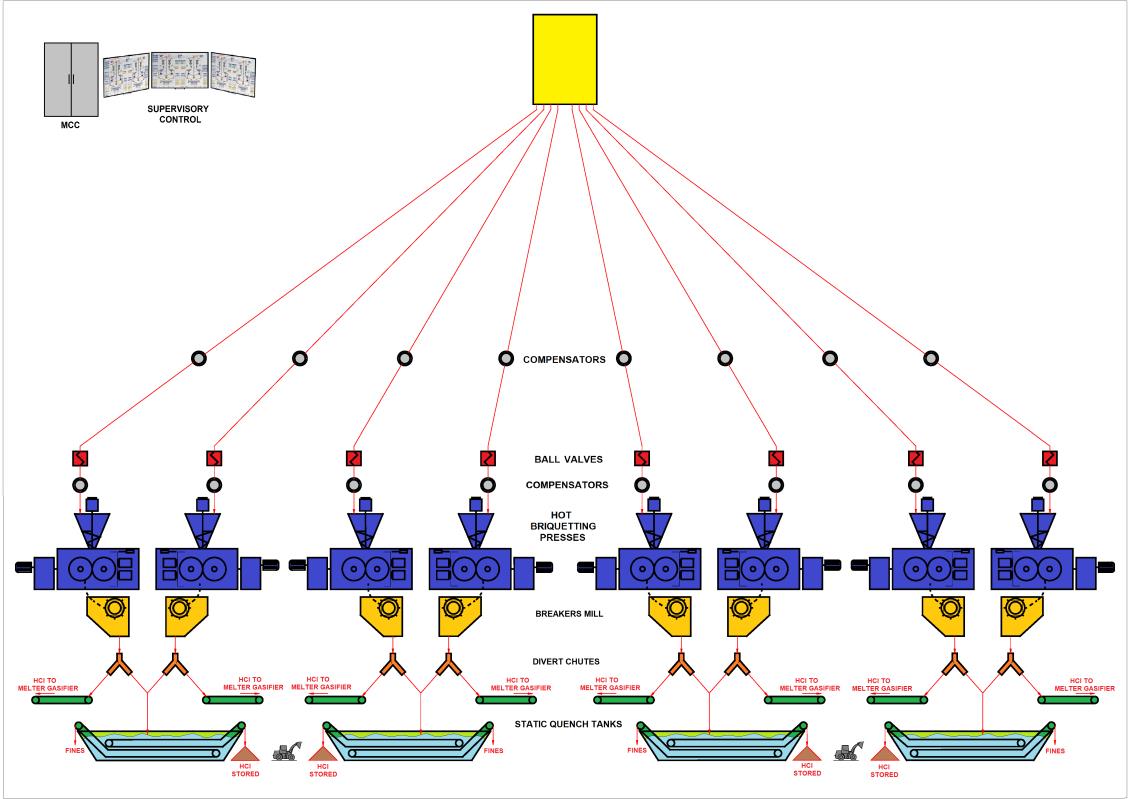
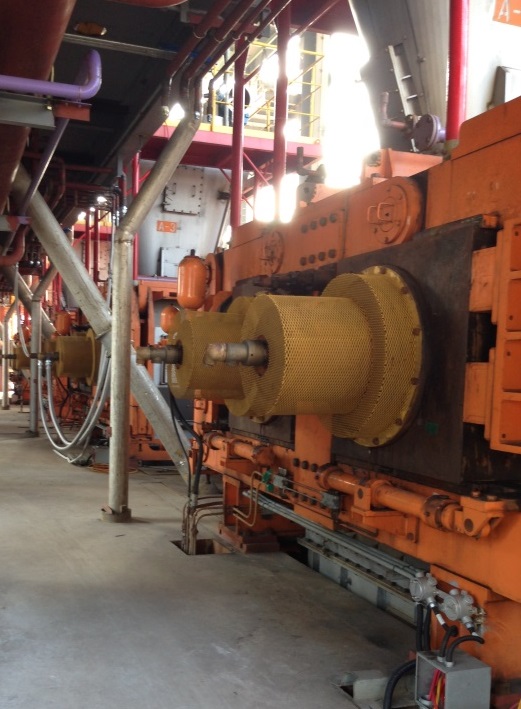
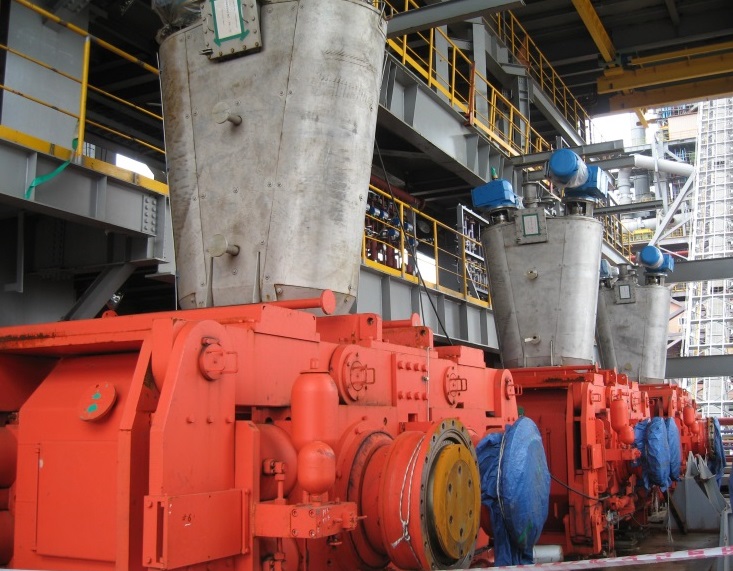
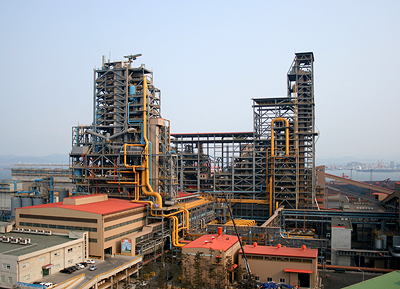
End-users' satisfaction with our HCI equipment
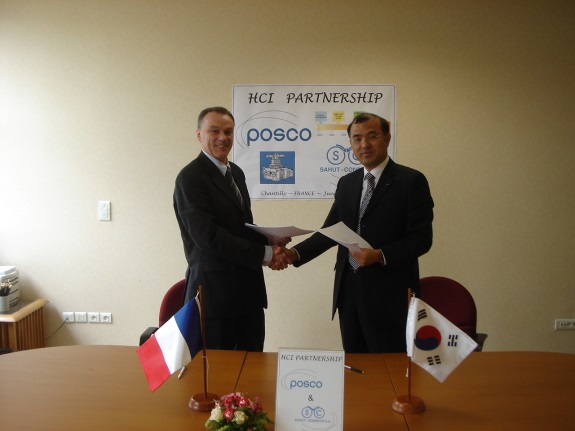
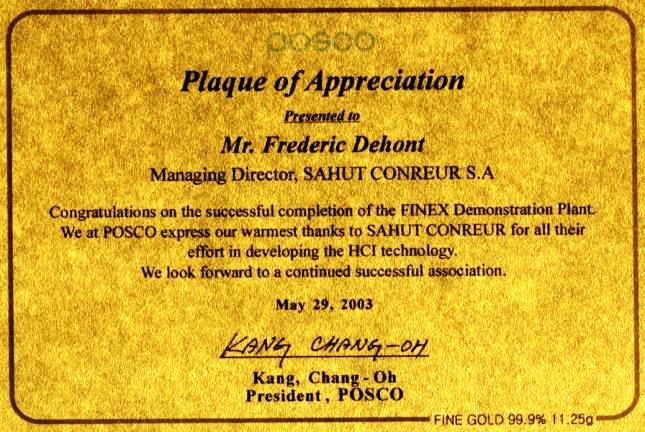
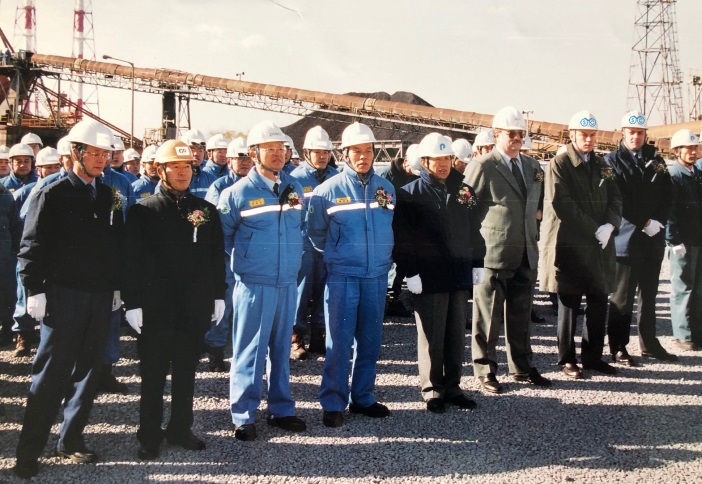